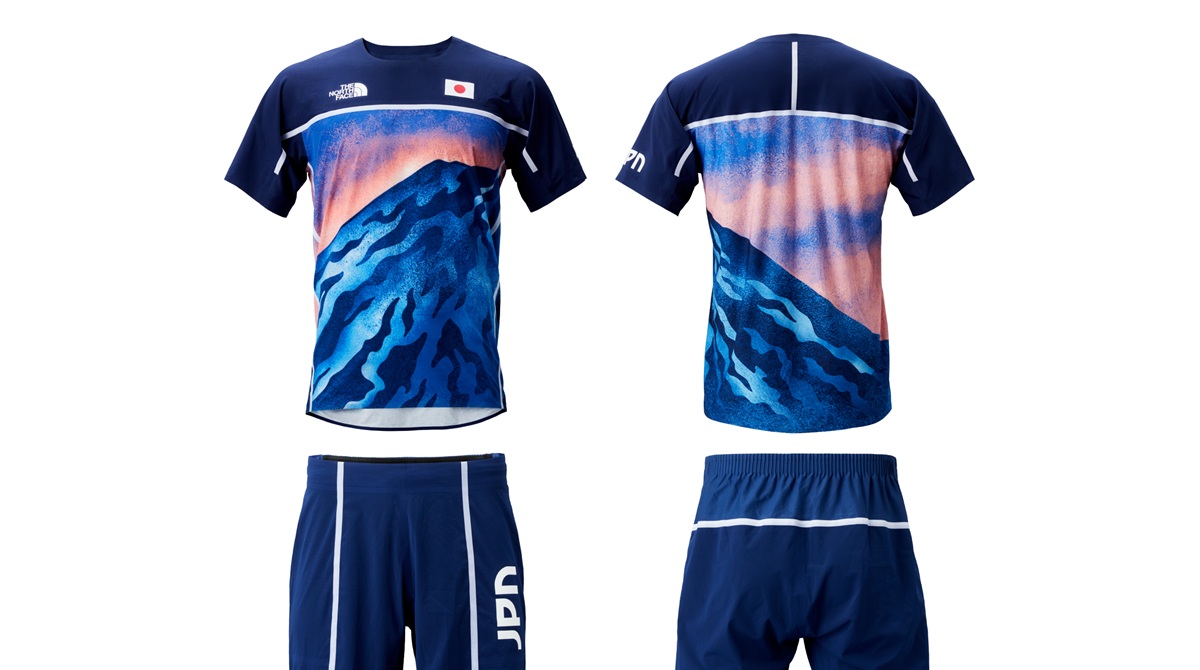
世界初のCO2由来パラキシレン・プロジェクト
この新技術とは、ポリエステルの原料であるパラキシレンについて、従来石油由来で作られていたものをCO2由来に置き換える試みだ。繊維生産の約6割を占めるポリエステルの原料がCO2由来に置き換えられた場合、ファッション産業におけるCO2の排出量は大幅に削減されることになる。国連からオイル産業に次ぐ環境破壊産業であると揶揄されるファッション産業にとって願ってやまない技術革新だ。この新技術の開発は富山大学、千代田化工建設株式会社、日鉄エンジニアリング株式会社、日本製鉄株式会社、三菱商事株式会社との共同開発であり、NEDO※で採択された国家プロジェクトだ。そして、ハイケムはこのプロジェクトにおいて、触媒開発と触媒のスケールアップ開発に従事している。
本日は、このプロジェクトに携わってきたC1ケミカル事業部の小西事業部長、代課長、ハイケム東京研究所の青島所長との座談会を通して、ハイケムの携わるCO2からパラキシレンを製造するプロジェクトの最新の状況やハイケムが携わる脱炭素技術の現在位置について聞いてみた。
※NEDO(New Energy and Industrial Technology Development Organization)
経済産業省所管の独立行政法人。国立研究開発法人 新エネルギー・産業技術総合開発機構
左から:C1事業部 小西秀明事業部長、ハイケム東京研究所 青島敬之所長、炭素イノベ課 代啓鵬課長
──今回、スポーツユニフォームにもなった、CO2由来のパラキシレンについて、この開発プロジェクトにハイケムが参画することになった経緯を教えてください。
代課長 まず、ハイケムは合成ガスからPET(ポリエチレンテレフタラート)の原料となるエチレングリコールの製造技術を確立し、中国で年産1,000万トン規模のライセンスに成功し、ラボレベルの技術を商業化に繋げた実績があります。
この延長線で、C1技術の権威であられる富山大学の椿教授と一緒に、合成ガスから様々な化学品を製造する技術の共同研究開発をやってきました。その中の1つが合成ガスからパラキシレンを製造する技術開発でした。
開発を進めるうちに、世界で脱炭素の機運が高まり、同様のコンセプトの触媒理念を活用し、原料をCO2に変更することに大手企業が興味を示してくれるようになったのです。
代課長「『非石油由来でPETを作れる世界で唯一の会社になる』という大きな目標というかコンセプトができた」
パラキシレンはペットボトルや繊維の材料となるポリエチレンテレフタラート(PET)の原料です。PETのもう1つの原料である、エチレングリコール(EG)については、ハイケムは一酸化炭素由来のものは既に中国で量産化に成功していますし、CO2由来についても開発を進めています。
この2つの原料があれば、世界で約8,000万トン製造されているPETをCO2由来で作ることができるようになります。ここで、ハイケムが「非石油由来でPETを作れる世界で唯一の会社になる」という大きな目標というかコンセプトができました。
小西部長 数ある大企業に並んでハイケムがなぜこのプロジェクトに参画できたのかというと、やはり一酸化炭素由来の合成ガスからエチレングリコールを作るという、日本で古くから開発されていたけど、忘れられていた技術を掘り起こして、新たな技術として確立させて商業化レベルに引き上げ、量産化を成功させたという実績が認められたということに尽きると思います。
実験室レベルでできる技術って結構たくさんあるんですけど、商業化するために大量生産の段階になるとほとんど実現できていない。ハイケムはそれを実現した実績がある。しかもそれを中国という巨大なマーケットで実証できたことが本当に大きい。実は私もそこに惹きつけられて、ハイケムに入ってきたうちの一人だからよく分かります(笑)。
青島所長 私は今年の4月にハイケムに入社したのですが、東京研究所や南通研究所において、わずか10年足らずという短期間でSEG®触媒の商業化を実現し、これだけ大きな事業に成長させた点にハイケムの大きな底力を感じます。これだけ事業を大きく成長させたノウハウをこのプロジェクトにも活用することを期待しています。
小西部長 もう1つの大きな理由は、ハイケムがパラキシレンやエチレングリコールの最大の需要国である中国にアクセスがあるという点です。そもそも、技術開発の大きな理由は商業化であり、需要があるところで開発を進める必要があります。現在PETの最大の生産国は中国であり、パラキシレンの需要は今、中国にあります。その「需要国である中国と技術をつなげる力があるのがハイケムだ」ということで、注目が集まったのではないでしょうか。
──改めてCO2由来のパラキシレンの技術開発においてハイケムの役割を教えてください。
代課長 プロジェクト発足当時からハイケムの役割は、触媒開発を起点にした触媒工業化技術の開発です。要は、触媒を大量生産し、工業化するプロセスの開発です。
小西部長「触媒の開発はチャーハンに似ている。いざ大きな鍋で作ろうと思うとなかなか再現できない」
小西部長 触媒ってよく「チャーハン」みたいなものだといわれています(笑)。
秘伝のたれと有名シェフのレシピがあって、同じように作ってもおいしくならないじゃないですか、チャーハンって。実験室レベルで完璧な触媒が完成したとしても、いざ大きな鍋で作ろうと思ったらなかなか再現できないものなんです。工業化するためには、その秘伝のレシピを大量に作れるレシピに変えて、ちゃんと皆から「おいしい」とか「再現できている」といわれるようにしなければいけない。しかも何回やっても同じ味を再現できないといけない。チャーハンもそうですが、触媒についてもこれが本当に難しい。
青島所長 そうですね。それに加えてプロセスにあった触媒の形状を設計する技術開発も必須となります。そして、ここはもう完全に企業しかできない。ハイケムはエチレングリコールの量産化の実績があってその辺のノウハウを有しているのも大きな強みだと思います。
──現在、CO2由来パラキシレンの技術開発は量産化に向けて開発中だと思うのですが、今はどの辺まで開発が進んでいるのでしょうか?
代課長 2020年にNEDOのプロジェクトが発足し、2023年3月に千代田化工のパイロットプラントからCO2由来のパラキシレンの単離に成功しています。そして、今回スポーツウェアに採用されました。最終的なプロジェクトとしては、2030年前後の商業化を目指しています。
青島所長 脱炭素技術の共通課題として、今はまだCO2や水素の調達に課題がありますが、これが2035年とか2040年ぐらいになってくると、また世界が変わっているだろうと思います。その時にすでに技術を持っているかどうか。その時に慌てて技術開発するのではなくて、今からその技術は持っておくっていうのは賢いやり方なんじゃないのかなと思っています。
──ありがとうございました。その他にも、現在、ハイケムが取り組む脱炭素技術の進捗についても教えてください。
小西部長 CO2由来のエチレングリコールの製造については、グリーンMEGとして現在開発中で、こちらもまさに商業化に向けた取り組みを行っているところです。現在市販されているエチレングリコールと同じくらいの価格帯を実現できる場所や規模で製造が可能となるよう、現在鋭意取り組みを行っているところですね。
青島所長「これから世界で求められるのはハイケムが実践してきたような商業化や実用化をいかに進められるか」
青島所長 脱炭素ということでいえば、このプロジェクト以外にもバイオマス由来のプラスチックについても取り組みを進めていて、先日は、北海道大学とハイケムが共同研究を進めるラボを開設したところです。これらのバイオマスの活用技術は先行して開発が進んでいますがまだまだ多くの開発技術が残されており、一般的な普及には至っていないのが現状です。
これから世界で求められていくのは、ハイケムが実践してきたような市場や生産拠点のネットワークを活かし、商業化や実用化をいかに早く進められるかにかかっているのだと思います。
小西部長 そういう意味では、ハイケムと組むことで実用化や商業化につなげられると思っていただけるよう、これからも特に環境分野において大きな実績を積み上げていきたいですね。