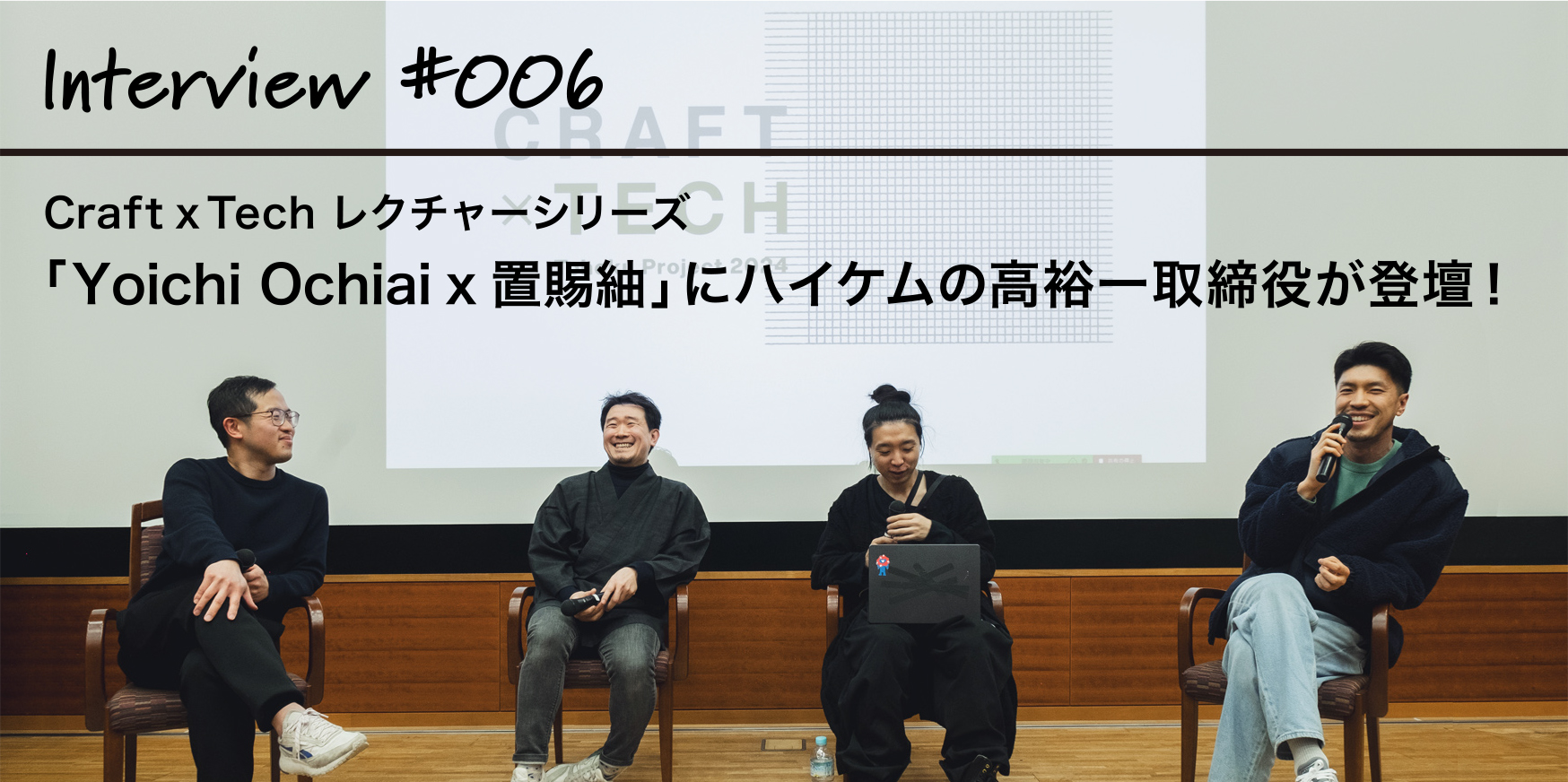
写真:SHUHEI. W
今回のイベントでは東京大学先端科学技術研究センターの吉本教授ファシリテートのもと、研究者・メディアアーティスト・起業家という複数の顔を持つ落合陽一さん、山形県の伝統的な織物「置賜紬(おいたまつむぎ)」の作り手である、株式会社新田の代表取締役社長である新田源太郎さんによる講演が行われました。講演ではお二人の素晴らしいチームワークを垣間見ることができ、これから起こるシナジーに期待感が高まる内容でした。
その後、お二人の講演に高も参加させていただき、会社の紹介や繊維産業の未来についても少し語らせていただきました。落合さんの絶妙なコメントもあり、興味深い鼎談となりました。ぜひご一読ください!
ハイケム=CO2から繊維を作る技術開発を目指している会社
ハイケムさんのご紹介をお願いできますか?
ハイケムは僕の父と母が作った会社です。
今は帰化していますが、二人とも中国人で、文化大革命が終わった1期生として中国の大学に入り、卒業してからは中国で商売を始め、その蓄えをもって日本行きのチケットに変えました。二人とも化学を専攻していたので、こちらの東京大学の化学の修士課程を修了し、その後現在の三菱化学(旧三菱油化)の研究職として働き、25年ほど前に夫婦で化学の専門商社としてハイケムを起業しました。
父親の専門分野はC1ケミカルという分野で、炭素をいかに物質に変換していくかということを愚直に研究している人です。その中で、ハイケムが持っている一番特徴的な技術に、CO(一酸化炭素)からポリエステルの原料を製造する技術があるのですが、昨今、世界中がカーボンニュートラルやグリーン化を求める中で、このCO(一酸化炭素)をCO2(二酸化炭素)に変えるような技術開発を行っていきたいと考えています。いわば、CO2から繊維の原料になるポリエステルを製造するということを目指している会社です。
すごいですよね。高さんのお話を初めて伺ったとき、CO2から繊維を作るというような錬金術みたいな話が、ほとんど実証されていて実用化に近づいているというのに本当にびっくりしました。
この錬金術を実現するためには、COをCO2に変えるという新しい技術が必要になります。この技術については、現在開発中で実証段階にあり、実用化はいつでも可能です。ただ、そのプロセスを導入することでコストが跳ね上がって、ポリエステルの価格が10倍くらいになってしまう。化学産業って、巨大な装置産業で利幅も薄いので、顧客がコミットしない状態では実用化は少し難しいんですよね。
なので、今はハイブランドやスポーツブランドなど製品に付加価値を付与できる企業との協業が面白いのかなと思っています。この取り組みがうまくいけば、CO2から作られた服なんかが皆さんの生活に普通に入ってくる日も近いかもしれません。
意味のCO2で付加価値をつける
繊維の未来を感じますね。
落合さんもそのような話を聞かれたことはありますか?
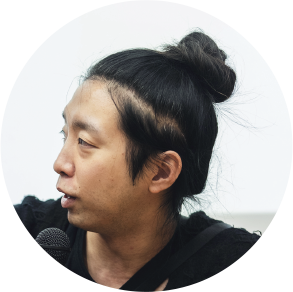
カーボンリサイクルの話ですよね?わりかし繊維系はあるかもね。
ただ、だいぶコストの問題が大きい。
僕は写真屋なので、写真を印刷する時に温泉で作ったり、死海の塩で作ったりするんですが、なんのCO2で作るかが結構ポイントになりますね。
どういう意味ですか?
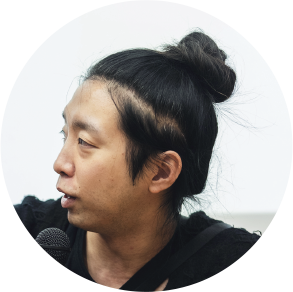
火葬場でやったらいくらでも面白いCO2とれるかもね(笑)。
意味の空間でしかないわけですから。カーボンニュートラルって。
この空間がだいたい400ppmくらいですので、がんばって集めても糸1本作れるかどうか。いわゆる、工場の排ガスとか、CO2濃度が高いところのものを集めたほうが、CO2を原料にするには効率が良いんです。ただ落合さんが言うように、サステナブルな文脈で物を売りたい人達って、きれいなイメージのCO2を使いたいといったニーズがあったりします。
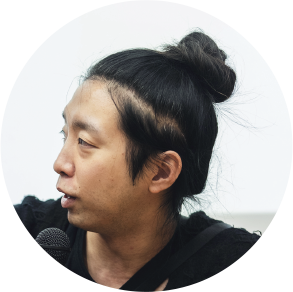
アイルトン・セナが出した排気ガスとかですね。
意味づけは面白いですね。
アパレルというのは日本の化学産業にとってすごく可能性があると思っています。化学産業ってリアクション産業で、川中にいるんですよ。大抵の化学品は石油から作られている。原料コストは石油屋さんが決めますし、出口はアパレルとか、生活用品を作っている人たちが決めます。あまり化学屋自体が、付加価値をつけてお客さんに渡す機会ってないんですよね。ただ、仮に空気から繊維を作れる技術を開発できるとしたら、自分たちが川上の存在として直接出口のアパレルなんかに販売ができるようになる。そういう時にCO2の意味づけって生きてくると思います。
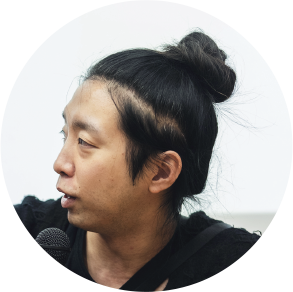
どれもCO2なのに(笑)。
同じCO2のはずなのに、意味のCO2が違うから、こっちのCO2の方が安全とか、他の動物が聞いたら、結構びっくりするような話ですね。
日本の伝統工芸の技術力で開発に成功した、ポリ乳酸(PLA)繊維
ついでに紹介させていただきたいのが、僕が今着ているジャケットは植物のデンプンから100%作ったものです。これ自体はトウモロコシのデンプンを一回発酵させて乳酸にするんですね。その乳酸を重合してポリ乳酸(PLA)という素材を作ります。
バイオ系のサステナブル素材だと、ビーガンレザーだとかは皆さん聞いたことあるかもしれないですね。
ただ、そういったものと比べてトウモロコシは世界中で大規模に生産されているという点でその優位性は大きいんです。サステナブルにするためには、必ず日常に落とし込んで、価格が手の届くものになっていかなければならないと思っています。
一方で、ポリ乳酸(PLA)には大きな課題がありました。トウモロコシのデンプンから作られているので、熱に弱いということです。繊維って高温で染色するので、ポリエステルと同じ温度帯で染めようとすると、色が入らずにボロボロになっちゃうんです。どうしようかなと困っている時に、日本の伝統的な織物屋さんや染物屋さんに頼んだらきれいに染まったということがありました。
ここら辺は、本当に日本の伝統工芸が持っている、言葉にできないような力、民族性とかそういう話になるのかなと思います。たぶん他の国で同じことをやってもできない。日本の伝統工芸って、「できるまで絶対やってやろう」みたいなマインドセットが、やっぱり他の国とは違うなと思います。振り返ってみると弊社にもクラフトテックさんの取り組みと繋がっているポイントがあるなと思いました。
なるほど、本当にそうですよね。
新田さんもこういう、工業的な繊維産業の人たちとの取り組みとかはあったりしますか?
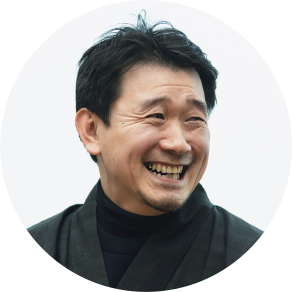
弊社は基本的には絹の素材を扱っているのですが、米沢が繊維に関する研究を江戸時代から盛んに行っていた土地柄もあるので、常に新しい挑戦はしていきたいと考えています。例えばレーヨンだったりポリエステルだったり、絹以外の様々なものにトライして新しいものを生み出すということには興味があります。
基本は絹ですが、様々なことにトライして新しいものを生み出すこと。それが結局自分を知ることに繋がるのかなと思っています。
こういうことをきっかけに、ハイケムさんとのコラボレーションももしかしたらあるかもしれないですしね。
こういうコラボレーションがどんどん広がっていくということが、このクラフトテックのプロジェクトの目指すところですからね。
(左から)
吉本英樹
東京大学先端科学技術研究センター先端アートデザイン分野、特任准教授。デザインスタジオTANGENT創業者。デザインとテクノロジーを融合させる手法で様々な作品を発表し、世界的ブランドにも多くのデザインを提供。「Craft x Tech」の発起人・総合プロデューサーであり、自身も参加クリエイターの一人。
新田源太郎
1980年、山形県米沢市に生まれる。2003年、京都老舗帯屋にて着物・織を学ぶ。2005年、株式会社新田に入社。日本伝統工芸展「新人賞」、米沢市芸術文化協会「協会賞」、MOA岡田茂吉賞「新人賞」、日本工芸染織展「東京都教育委員会賞」、他多数受賞。LEXUS NEWTAKUMI PROJECT 2017 山形県代表。2017年、株式会社新田代表取締役社長(5代目)に就任。公益社団法人日本工芸会 正会員。
落合陽一
メディアアーティスト。1987年生まれ、2010年ごろより作家活動を始める。境界領域における物化や変換、質量への憧憬をモチーフに作品を展開。筑波大学准教授、デジタルハリウッド大学特任教授。2025年日本国際博覧会(大阪・関西万博)テーマ事業プロデューサー。
近年の展示として「おさなごころを、きみに(東京都現代美術館、2020)」、「北九州未来創造芸術祭 ART for SDGs(北九州、2021)」、「Ars Electronica(オーストリア、 2021)」、「Study:大阪関西国際芸術祭(大阪、2022)」、「遍在する身体、交錯する時空間(日下部民藝館、2022)」など多数。また「落合陽一 x 日本フィルプロジェクト」の演出など、さまざまな分野とのコラボレーションも手かげる。
高裕一
1986年生まれ。中国の復旦大学を卒業後、宇部興産(現UBE)を経て2014年、ハイケムに入社。2022年1月、ハイケム株式会社 取締役及びサステナベーション本部長に就任。
Craft x Tech(クラフトテック)について
https://www.craft-x-tech.com/
東京大学の先端科学技術研究センターなどが推進する、日本の伝統工芸と現代的なテクノロジーを繋ぐ新しい試みです。伝統工芸の各産地と、世界的に活躍するデザイナー・アーティストによるコラボレーションをプロデュースすることで、時に数百年という歴史を持つ工芸に新しい発見をもたらすことを目指しています。第1回となる、Craft x Tech 2023では、東北6県の6産地と、クリエイター6名によるコラボレーションが実現しています。