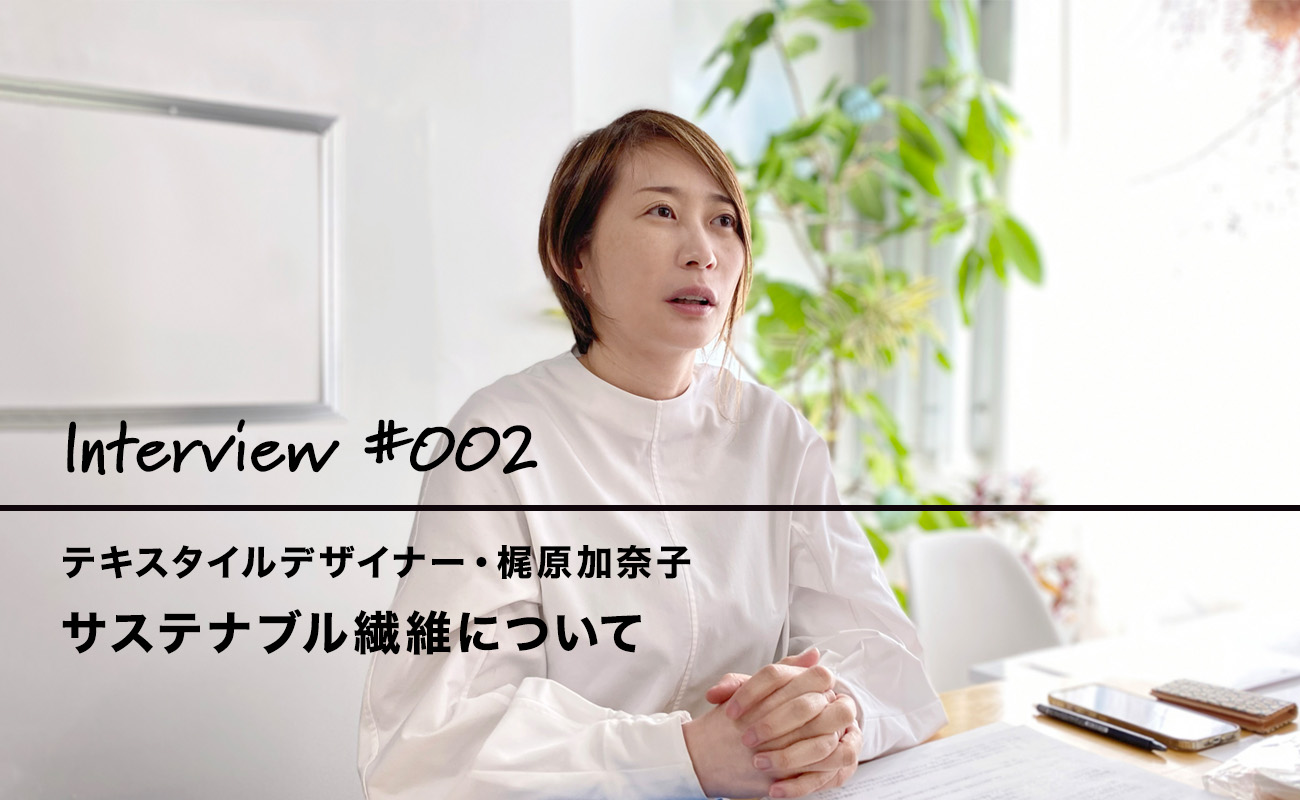
世界的テキスタイルデザイナー 梶原加奈子氏に聞く
ハイケムは、昨年次世代のPLA繊維「HIGHLACT®(ハイラクト®)」を発表し、国内外に向けたPLA繊維の市場開拓に拍車をかけた。洋服の廃棄問題などでサステナブルな洋服の開発にアパレル各社が動き始めた今、果たしてPLA繊維はその渦中にいるテキスタイルの専門家の目にどのように映っているのだろうか。そして、PLA繊維のまさに競合となるサステナブル繊維にはどのようなものがあるのか。そんな私たちの疑問に答えてくださったのは、海外ラグジュアリーブランドに生地を販売するルートを持つ世界的テキスタイルデザイナーの梶原加奈子氏。グローバルな視点でファッションやテキスタイルに深い見識を持つ梶原氏が注目するサステナブル繊維を紹介する。
CEO クリエイティブディレクター 梶原加奈子氏
北海道札幌市生まれ。多摩美術大学デザイン学部染色科を卒業後、(株)イッセイミヤケテキスタイル企画に入社。退職後渡英し、英国の王立芸術大学院、RCA Fashion & Textile courseにて修士課程を修了する。在学中に、グアテマラの織物工場の製品をイギリスの市場に繋げるといったディレクターの仕事に従事し、「デザインとは人や社会を繋ぎ未来の架け橋になる職業である」ことを実感しやりがいを見出す。また、欧州新人登竜門のデザインコンペTEXPRINT2005にてグランプリを受賞し、フリーランステキスタイルデザイナーとして海外で活動する道が拓けた。卒業後、今後の方向性を探る中で日本の繊維市場が厳しくなることを見越し、日本の産地立て直しに貢献したいという思いから帰国。2006年に(株)KAJIHARA DESIGN STUDIOを設立し、日本繊維産地の未来づくりに貢献することを目標にグローバル販路の開拓、トレンドマーケティング、地方活性化に向けた新規事業ブランディングに携わる。
——テキスタイルデザイナーとはどのようなお仕事なのですか?
梶原 私は主に欧州のハイメゾンに素材を供給するルートを築いてきたので、日本の提携工場で開発した生地を提案したり、ハイメゾンからの要望に応じて日本の生地をリサーチして提案するといった架け橋の仕事をしています。また、2015年以降は、日本の繊維工場から製品ブランドを立ち上げたいというニーズが多くなり、いわゆるDtoC製品の総合ブランディグに関わる仕事にも注力しています。
——メディアでの露出を拝見すると、サステナブル繊維の専門家としても活躍されているようですが?
梶原 欧州では2016年頃から政府の影響もあり、素材展示会のコンセプトがサステナビリティを中心に変化しました。欧州ハイメゾンやアメリカブランドの方々から「サステナブル素材の提案を増やしてほしい」という意見も増えてきて、素材開発を強化し始めました。一方で、当時日本では「サステナブルを意識した糸や加工を取り入れると価格が高くなり、販売に向けてリアルじゃない。ユーザーのニーズではない。コンセプト倒れだ」といったネガティブな意見が大半でした。そんな日本も近年の台風や気温上昇など気候変動の実感や、コロナ問題を通して、温暖化現象や環境破壊の情報が社会の中で広がりつつあり、学校でも教育が始まり、サステナブルに対する意識が少しずつ変わってきていますね。中国でもこの流れは確実に来ているのではないかと思います。現に私の携わるプロジェクトも2021年よりサステナブルに関わるものが一気に増えました。
——現在、ポリエステルやコットンが繊維生産量の大半を占めているわけですが、現状のこの繊維の構成をどのような状態にすることが、繊維業界にとってのサステナブルなゴールになると考えますか?
梶原 繊維業界が目指すところはいずれ二つに集約されると思います。一つは「土に還る素材に変えていくこと」もう一つは、リサイクルを続けて廃棄物を減らし「サーキュラーエコノミーを実現すること」です。
——それらを実現するにあたって、梶原さんが注目されているサステナブル繊維について教えてください。
主原料が天然素材で、『植物繊維』と『動物繊維』の2種類に分けられます。主原料がコットン(綿)・リネン(麻)など植物によるものを『植物繊維』といいます。また、シルク(絹)・カシミヤ(山羊)・ウール(羊毛)などを主原料とするものを『動物繊維』といいます。
リネン(麻)
梶原 植物性の天然素材の中では、リネン、ヘンプ、ジュート、ペーパー糸が注目されています。カーボンニュートラルを実現していくためには緑を減少させないことが必要です。その点これらの原料の植物は伐採しても成長が早いため環境への負荷が少ないです。また水も多く使わずに育つのも良いですね。天然素材の中ではコットンの使用量が多いと思いますが、これからのグローバル市場では麻系の素材が積極的に使われる傾向が高まっていくと思います。
サステナブルシルク
梶原 動物繊維では動物愛護の問題が前面に出てきてしまいますね。無農薬の桑の葉を食べるといったサステナブルシルクもあるのですが、虫であっても生命なのでSDGsではないと捉える人がいることは事実です。そこで、シルクにおいても蚕を殺してしまう前に取り出して、残った繭を糸にするピースシルクという糸が注目されています。
主原料が石油・人工的に作られる高分子からなり、『合成繊維』と『再生繊維』の2種類に分けられます。ポリエステル・ナイロンなどは、石油系を原料とする『合成繊維』、レーヨン・テンセルは天然の木材などから精製された『再生繊維』です。
リサイクルポリエステル
梶原 欧州市場ではケミカルリサイクルに注目が集まっています。フランスでは2022年1月より衣料廃棄禁止令が施行されています。そこで街中に洋服の回収ボックスが設置されるようになりました。服から服のリペア、リユース、リサイクルの需要は今後益々伸びてくるでしょう。ただ、ケミカルリサイクルできる設備が世界でまだまだ少ないのが現状です。日本と中国にプラントが一つずつしかありません。日本でももう少しプラントが増えないと国内リサイクルの体制は語れないと思います。そして、リサイクルの際に大量のエネルギーが必要になってくるのでカーボンニュートラルに貢献する側面ではまだ解決できない課題も残しています。
再生繊維 キュプラ・リヨセル
梶原 土に還る素材ということで注目しているのは天然の木材などから精製される再生繊維です。業界の中では旭化成が「ベンベルグ」という商標名で世界的なシェアを獲得している『キュプラ』やオーストリアのレンチング社が製造する「テンセル」に代表される『リヨセル繊維』です。特にレンチング社はサステナブルな企業として定評があるので生地を採用する際にも安心感があります。また、伐採までに適切に管理された森林から調達した木材を使用しており、FSC(森林)認証も取得しています。
次世代セルロース繊維の大本命 レーヨン素材「クウラ(KUURA)」
梶原 レーヨンはもともと絹の代わりの繊維として、最初に開発された化学繊維です。ただ実際には生産工程で有機溶剤を使用しており、特にレーヨンを作ることは年に1回爆発する危険性があるといわれるほど。このクウラは、伊藤忠がフィンランドの木材パルプ世界最大手のメッツァグループ(METSA GROUP)と共同で開発するレーヨンです。コストもほぼ変わらず、危険性の少ない画期的な製法で製造しているため次世代セルロース繊維の大本命ともいわれています。FSC認証他多数の認証も取得しており大変有望なのですが、まだ大量生産の目途は立っていないようです。これからの発展に期待したいです。
生分解性繊維 PHA(PHBH、PHBVなど)
梶原 バイオポリマーの中でも海洋分解性を有するPHAには大変注目しています。ナイロンの代わりに海洋汚染しない漁網などを開発できるとよいかもしれませんね。また、身近なところでいうと、合成繊維を洗濯することで、海に流れ出すマイクロプラスチックの量は無視できない量であり海洋環境への影響が懸念されています。特にフリースから洗濯によって流れ出してしまうことは懸念されており、PHAでできた適正価格の範疇に収まるフリースが開発されると、サステナブル意識が高いブランドやユーザーには人気が出てくるのではないでしょうか。ただ、PHAも量産化が難しかったり、樹脂の性質上繊維化した時の物性の問題があったりするようなので、更なる改良が進むことを期待しています。
PLA繊維
梶原 PLA繊維はまだアパレルの中では中心素材となってはいませんが、今後ますます注目されていくと思います。石油由来であることや土壌分解しないポリエステルの問題点を解決してくれる「ネオ・ポリエステル」といえるのではないでしょうか。今まで問題であった熱に弱い特性を改善した糸が出来ており、量産化に期待できるという点でもよいですね。
——PLA繊維にも注目頂いていますが、PLA繊維の現時点での課題は何であると思われますか?
梶原 良くも悪くもポリエステルに近いというのが問題なのではないでしょうか。昔の合成繊維という雰囲気なんですよね。以前のPLA繊維は熱に弱かったため加工の開発が十分に進んでいない印象です。触ったときの風合いの魅力が乏しいですし、いま合繊で求められている天然調の雰囲気がない。糸や素材開発におけるデザインのバリエーションもまだ少ないというのが印象です。長繊維か短繊維か。光沢感やマット感、張り感や柔らかさなどいろんなバリエーションが開発されると使いやすくなります。個人的には、PLAは土に還る繊維ということで天然繊維に近い風合いが表現できることを期待しています。
また、ポリエステルが必要な服はどちらかというとスポーツ業界に多いと思います。スポーツウェアでは、吸水速乾や透湿防水、撥水、UVカット、抗ピリング、防透など様々な機能性が求められます。PLAがポリエステルの品質数値と近いところまで研究がなされていくと関心が高まるのではないかと思います。
PLAのコンセプトをいかに簡単に消費者に伝え、いかに社会に浸透させていくかも課題です。価格のメリットを検討することはまだ難しいだろうと思います。ですから付加価値をどう伝えて価値だと思ってもらえるのか、言葉とかデザインの力が必要になってくると思います。それには下げ札やポップなどの開発が必要になってくるでしょう。
——PLA繊維を供給するハイケムに期待することは?
梶原 熱に強いポリ乳酸の樹脂を安定供給できるというのは御社の大きな強みですね。糸のバリエーションを展開し、日本の工場と共に織物や編物やテープ資材など素材デザインの可能性を広げて欲しいと思います。地方にはまだまだ高い技術をもった繊維メーカーがたくさんあります。彼らと組むことで、PLA素材の新たな未来が切り拓けることを楽しみにしています。洋服だけでなく、次世代の暮らしに関わる様々な分野の素材やプラスチック製品が植物由来に変化していく可能性を秘めていると思います。