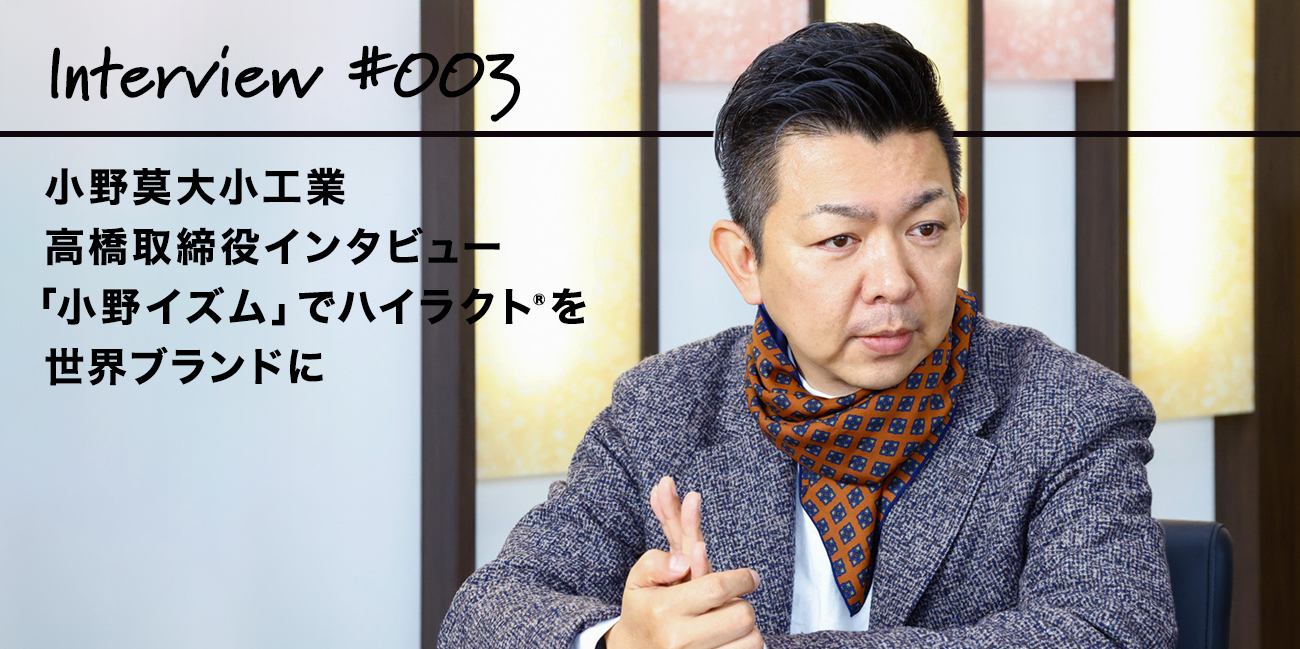
Interview with Director Takahashi of ONO MERIYASU KOGYO CORP
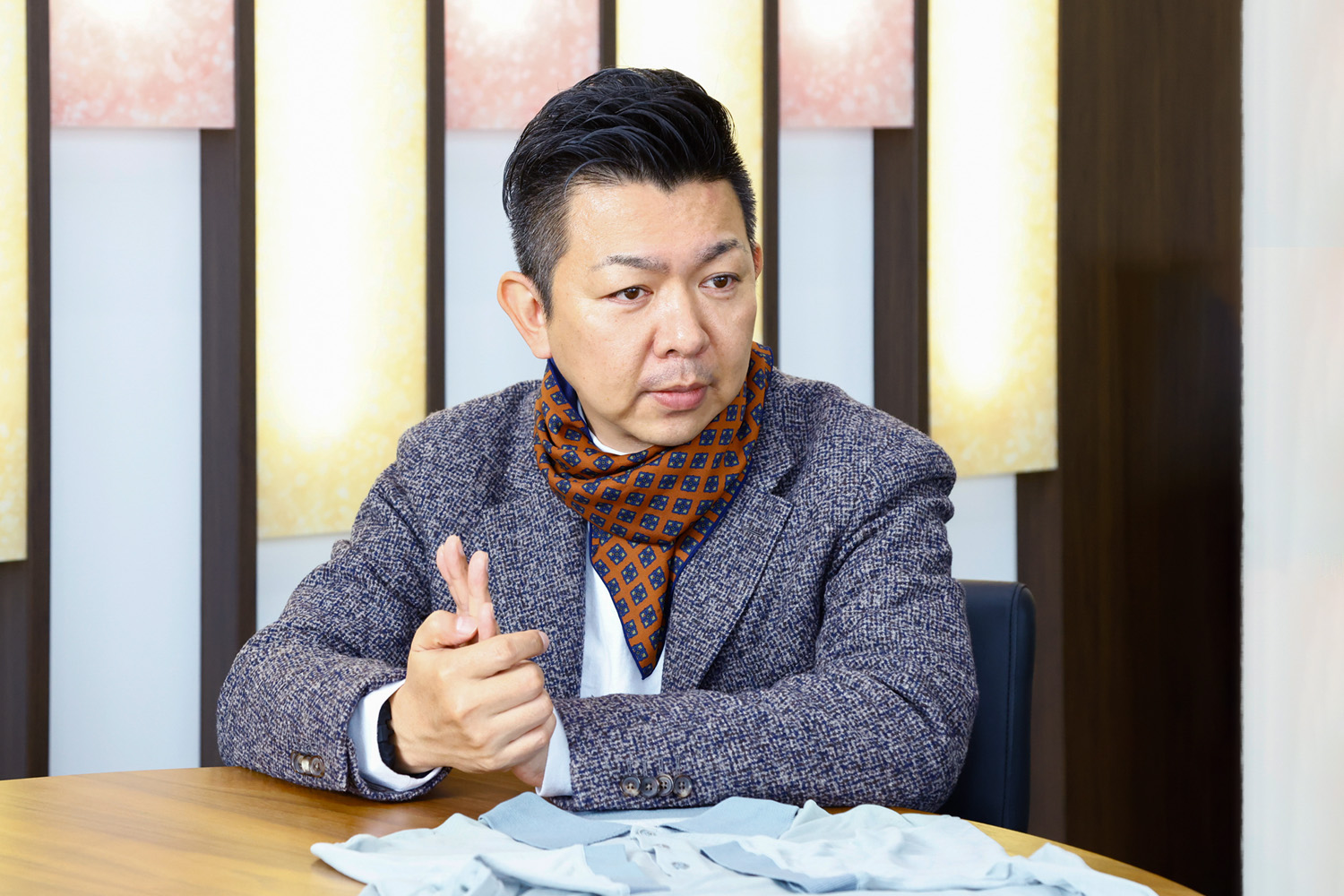
——First, I would like to hear about the history of ONO MERIYASU KOGYO. The company was founded in 1924 (Taisho 13), right?
Takahashi: It was the year after the Great Kanto Earthquake. The founder was the father of the current president, Mr. Tetsugoro Ono, who was originally a large landowner in Hirai, Edogawa Ward, Tokyo. People who were affected by the earthquake in the center of Kanto sought refuge in the suburbs of Hirai and fled there, and Tetsugoro, who was a large landowner, provided food and places to sleep. Of the people, one of them was selling knits with a knitting machine loaded on the carrier of a bicycle. Everything was burned in the earthquake, so it must have been very useful for underwear and children’s clothes. The founder, who thought this could be a business, got a machine from that person and founded a knitting factory for round knitted meriyasu fabric using a hanging knitting machine.
——I see, the company was a knitting factory at the time of its founding. How did it evolve after that?
Takahashi: At that time, the center of the textile industry was in the Kansai region, and there were no companies manufacturing knitting machines in Tokyo. In such a situation, the founder, Mr. Tetsugoro Ono, thought about “how to make good fabric” and decided to develop a knitting machine. And what was born was the “Ono-style fleece knitting machine”.
The “Ono-style fleece knitting machine” installed at the ONO MERIYASU KOGYO Factory Sahara Factory
Ordinary knitting machines are machines made to “make quickly and in large quantities”. Therefore, the fabric that comes out is small in stretch, thin and flat, just like mass-produced fabric. However, the founder’s team was committed to “making good fabric”, even if the efficiency was a little poor. And they created a machine that knits a fabric that is very stretchy, like rubber, with tight stitches. At that time, rubber was expensive and hard to get, so the highly stretchable fabric that could be made with only cotton was very useful. In fact, the fabric knitted with Ono-style fleece does not lose its shape even after many years of use, and can create a knitted fabric that fits the body with only using cotton. And this knitting machine is still used for unique fabric making, even now that they have started planning and selling fabric products.
——Indeed, I can already feel the “Ono-ism” from here (laughs). And the representative work of ONO MERIYASU KOGYO is undoubtedly “Cosmolama”.
Takahashi: Yes, indeed, it was “Cosmolama” that made our company recognized in the world. The fabric is special, and branding by naming the fabric and thread was also a rare attempt in the industry.
Cosmolama: A super-thin cotton cut-and-sew made with 100% of the highest-grade extra-long cotton from India, and subjected to ONO MERIYASU KOGYO’s unique special processing with strong twisted yarn. It is characterized by a delicate touch with a crisp feeling, elegant gloss, and drapability. Thanks to the technology of making our own yarn, we have achieved “fastening-free” where the fabrics do not stick to each other, and obtained a patent in 2009.
——Where did the idea for Cosmolama come from?
Takahashi: Actually, the idea came from the “feather robe of a Buddha statue”.
The current president loves shrine and temple tours, and he loves Buddha statues. So, the beginning was when he thought, “I want to create a thin fabric like a feather robe with cotton.” The president’s development theme is The president's development theme is "to express everything from a silk to wool feel using 100% cotton." I think the president is more of an artist than a fabric maker.
——That’s amazing. It seems to be packed with various commitments.
Takahashi: Yes, “Cosmolama” is particularly committed to “cotton” selection and “thread processing” centered on the highest quality raw materials. The fabric we make is, if you will, “Traditional Sushi”. It’s not a revolving sushi at all, everything is original. While other companies are asking how much they can make cheaply and efficiently, we are a little different. What the president often says is, “If you want to make a first-class thing, you have to use first-class materials.” Regarding the selection of materials, the president orders samples from various production areas such as India, knits them in actuality, and checks the touch before adopting them. Also, for thread processing, we go through a lot of processes before actually putting it on the knitting machine.
——That’s amazing. I heard that Mr. Takahashi is a contributor to overseas expansion. Why did Mr. Takahashi join ONO MERIYASU KOGYO in the first place?
Takahashi: It’s been 20 years since I joined the company, but before joining the company, I was a clothing salesperson after graduating from university. In the midst of that, I wanted to be involved in manufacturing and joined our company. What I felt when I joined the company 20 years ago was that there were too few people who liked fashion and were involved in fabric making. Everyone was thinking about how to make money, and they didn’t care about clothes. So someone like me joined the company and brought in a perspective of “clothes look cool if you do this.” I think that attitude is what led to the trust from each fashion brand.
——Why did you decide to embark on the development of PLA fiber “HIGHLACT®” together with HighChem?
Takahashi: The beginning was when overseas high maisons started saying that they would not adopt fabrics that were not sustainable. So, we also started looking for sustainable materials in our company. But I felt that everything was different. That’s when I met HighChem by chance.
PLA is a bit of a different genre among sustainable materials, isn’t it? It can be used not only for clothes but also for all kinds of plastic products, and I felt that there was no such interesting material. If we teamed up with HighChem, we thought we could do it, no, we were convinced that we could definitely do it, so we wanted to do it together. PLA is a material that I want to make the main one after Cosmolama, or I want to put it on the same page as ours.
——PLA is a difficult material to fiberize, but what was difficult when you actually handled it?
Takahashi: As everyone says, the weakness is that the strength of the thread and the heat resistance are low. This is still in the process of being overcome, but I think it is an achievement that we were able to make black fabric in one year. After all, PLA was said to be a material that should not be made into fibers…
・HIGHLACT® fabric (developed by ONO MERIYASU KOGYO CORP)
——Why do you think you were able to overcome it in just one year?
Takahashi: That is, without a doubt, the strong desire of the HighChem team and all of us to “do something about PLA.”
“I think
people don’t move without feelings.”
Even during the time of Cosmolama, in order to get into overseas high maisons, I didn’t know how to get to know the people at the headquarters, so I just kept calling the main store of the shop in Paris every day. Perhaps they felt sorry for me, one day, I was able to connect with the person in charge. When doing something difficult, you have to do something ridiculous like that, if you didn’t have a “strong feeling”, you couldn’t do such a thing.
——It’s been a year since the development, how is it?
Takahashi: Various styles of PLA fabric have been completed in this period of one year. The variation has increased compared to last year, and some apparel brands that have adopted us have also appeared. In that sense, the situation has improved considerably compared to December of last year. Not only the condition of the fabric, but also the increase in options has changed the reaction when showing it to the apparel people, and I have a feeling that PLA will be accepted in the market.
HIGHLACT® fabric
——Please tell us your future goals.
Takahashi: First of all, it is to be used by overseas high maisons.
The advantage of taking it overseas is that while Japanese people think “how efficiently to do it” first, people overseas think about, “how to sell the product at a high price.”Japan is the only country that can fully utilize the PLA, or rather, we are the only ones who can. So, first of all, we want overseas people to understand our efforts and digest them.”
From there, I want to aim for the step of 5 billion or so that HighChem is aiming for next. PLA can be substituted for various things, not just fabric, so I believe that the future where various things are replaced with PLA can definitely be realized.
It’s not a dream story, but we have to go that way. In the future, cars will definitely become EVs. One of the things that will change might be PLA. The world is constantly changing.
——It’s very reassuring to be able to push forward with ONO MERIYASU KOGYO CORP!
Takahashi: What I am looking for is to pursue “Ono-ism” without stopping. It’s Ono-ism to keep challenging ourselves and keep doing new things that no one else is doing.
Even polyester was “cheap and bad” at first, but it has developed into what it is now. The world is changing, so I think it’s about understanding that and seeing what to do next.