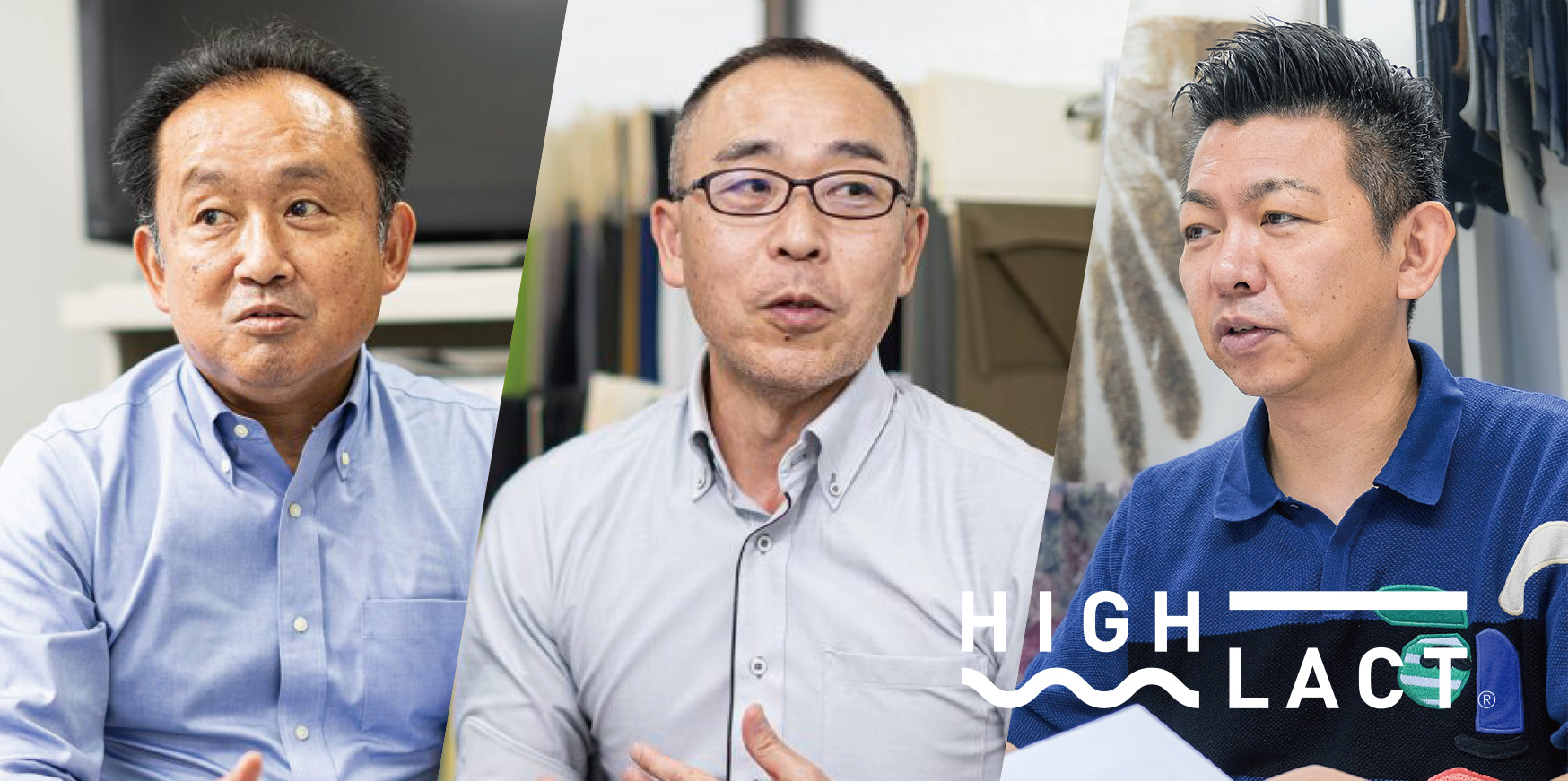
かつては不可能とまでいわれた深みのあるPLA100%のフィラメント糸によるフォーマルブラックの開発に成功した。この開発成功の鍵となったのは、日本のテキスタイル業界において、100年にわたる伝統を築き上げてきた企業の技術力だ。
今回、(株)ソトーの日化工場を訪れ、HIGHLACT®の開発において大きな役割を果たした3つの企業のキーパーソンにインタビューした。その舞台裏に隠された情熱と努力を紹介する。
お話を伺った人
染色加工事業部 日化工場 工場長 奥村 直規
会社紹介
1923年創業。尾州一宮の毛織物産地に100年根付く老舗の染色整理加工業界の大手。今回お邪魔した日化工場では、ポリエステルなどの合繊繊維やウール、コットンの染色及び仕上げの整理加工を行う。
染色と同時に生地に特殊な風合いを加える整理加工技術は国内外からの評価が高く、業界トップクラス。
常務取締役 高橋 幸太郎
会社紹介
1924年創業の老舗繊維メーカー。常に最高品質の生地を生み出し、革新的な方法で生地を開発する。2006年に発表された極薄のコットン生地「コズモラマ」は画期的な製造方法で生み出され、特許も取得。世界のトップメゾンからも採用されている。
サステナベーション本部 ファッション・アパレル部 プロダクトマネージャー 藤原
会社紹介
「日中の架け橋」として化学品の輸出入販売や受委託製造事業を行う化学の専門商社。生分解性材料を始めとする新素材の開発や市場開拓を行うとともに、C1ケミカル技術をベースとしたカーボンリサイクル技術の開発やライセンス事業、触媒の製造販売にも注力。
——HIGHLACT®で、PLA100%のフォーマルブラックに着手したのはなぜですか?
藤原 ファッション衣料として普及するには、黒や紺などの濃色を表現できないとダメなんですよね。ほとんどのアパレルはデザインの半分以上を黒または紺で構成しています。だから、ファッション衣料として定着するためには、黒を表現できないと認められない。
一方で、ポリ乳酸(PLA)は高温に弱いという特徴があって、高温での処理が難しいため、濃い色がうまく染まらないというジレンマがあった。だから、「黒はポリ乳酸(PLA)では表現できない」というのが長い間の業界の固定概念だった。ファッションとしてポリ乳酸(PLA)が普及しなかった最大の理由は染色にあったんです。その固定概念をなんとか打破したいというのがHIGHLACT®において、「PLA100%フォーマルブラック」を開発したきっかけです。
奥村 実は、もう何十年も前からポリ乳酸(PLA)繊維は開発されていましたが、その当時は白や薄い色しかなかった。またそもそもPLAのフィラメント100%のサンプルも少なくて、ほとんどが綿との混紡でした。
——今回のHIGHLACT®のPLA100%フォーマルブラックの開発における3社の役割を教えてください。
藤原 ハイケムの担当は原料を調達して糸を作るまで。生地の設計から、編み立てをして生地を作るまでが小野莫大小工業さんの役割です。そして、小野莫大小工業さんが製造した生地をソトーの日化工場さんで染色、仕上げの整理加工を行い、生地が完成するという流れです。
——どのような経緯でPLA100%フォーマルブラックの開発を実現したのですか?
ポリ乳酸(PLA)専用の染料の開発成功で世界が認めるフォーマルブラックが実現!
奥村 ハイケムさんが、ポリ乳酸(PLA)に改質剤を加えて樹脂の耐熱性を向上させたことで、当社でもポリ乳酸(PLA)の黒の染色への取り組みを開始しました。温度が高いほど染料の濃度を上げることができるので、ある程度までは染色が可能になりました。
当初は一般的なポリエステル用の黒の染料を使用して染色を試みました。黒をより深く見せるために、染料に赤みの成分を加えたり、様々な色素を細かく調合したりすることで、一番黒いだろうと思われるところまで持っていくことができました。それだけでも、ポリ乳酸(PLA)でここまで染色ができるようになったのかということで大変驚かれました。
一方で、ポリ乳酸(PLA)では、ポリエステルや綿がフォーマルブラックとして表現している黒と比べると少し赤身がかった表現しかできなかった。ヨーロッパでは、青みの強い黒でないとフォーマルブラックとして認めてもらえないんですよね。
藤原 これまではポリエステルなどに使う染料を、ポリ乳酸(PLA)に転用するというような考え方だったんですが、それがポリ乳酸(PLA)に向いているかっていうと必ずしもそうではなかった。そこで、ポリ乳酸(PLA)専用の染料の開発がスタートしました。
染料の開発にあたっては、染料メーカーさんと改質したポリ乳酸(PLA)にあう染料を開発しようということからスタートし、小野莫大小工業さんやソトーさんと連携し、意見交換しながら進めてきました。
染料メーカーさんが、ソトーさんの日化工場の方に度々訪問し、本社の試験室でも繰り返し実験を行いました。そして、ようやく1年の開発期間を経てこのターゲットに近いPLA100%のフォーマルブラックが完成しました。
(株)ソトー 日化工場の染色機
奥村 そうですね。ソトーでは、そのポリ乳酸(PLA)専用の染料に対して、どんな温度で染めたらよいのかとか、どんな後処理をしたらよいのかということを話しながら進めてきました。
——このPLA100%フォーマルブラックを実現するために、小野莫大小工業さんとソトーさんの方で工夫された点を教えてください。
高橋 糸から生地にする際に小野莫大小工業としてこだわっている点は、フォーマルブラックとしての生地の魅力をいかに引き出すかということです。
小野莫大小工業は「良い生地を作る」ことにこだわり、一流のモノづくりを心掛けています。ですから、編地にする際に糸の撚りを強くするなどひと手間加えます。
「小野式フライス編み機」
小野莫大小工業が独自に開発した編み機
高橋 特に、ポリエステルやポリ乳酸(PLA)などの合繊100%の生地では、横段といって、横方向に筋が出てしまうという不具合が発生することがあります。そのため前工程で丁寧な加工をすることで、不具合を防ぎ、より魅力的な生地に仕上げることができます。
奥村 黒い生地を染める際には、洗濯などで発生する色落ちについても考える必要があります。ポリ乳酸(PLA)は染色性もさることながら、色持ちもあまりよくなかった。この課題に対しても、ソトーの仕上げの加工技術を活用しました。
染色後の生地を乾かすためには、テンターと呼ばれる機械を使用します。通常、染色工場では、テンターの長さが25メートル程度です。しかし、通常のテンターでは生地を乾かすために高温が必要で、ポリ乳酸(PLA)には適さなかった。それに対して、ソトーの日化工場では通常の3倍の長さのテンターを保有しています。この特長は尾州がウールの産地であり、分厚いウールの生地を乾かす必要があるためです。
この特長を利用することで、高温を使わずにポリ乳酸(PLA)の生地を乾燥させることができ、PLA100%フォーマルブラックの色落ちを防ぐのに大きな利点となりました。
生地を乾かす工程に用いられる「テンター」
(株)ソトー 日化工場
——PLA100%フォーマルブラックに対する、お客様からの反応はいかがですか?
藤原 非常にいいですね。やっぱり、ポリ乳酸(PLA)100 %のフィラメントを作ることでポリエステルとは違ったポリ乳酸(PLA)らしさというのが生地の表情に出てくるのかなと思っています。ちょっとドレープ性があって、シルクのような光沢がある生地をポリ乳酸(PLA)のフィラメントを使って表現できている。そして、これを実現できたのは小野莫大小工業さんとソトーさんの100年続く技術力がなせる技なのだと思います。
——今後の展開を教えてください。
奥村 ポリ乳酸(PLA)の生地のバリエーションを増やしていくことです。この点においてはソトーの強みが発揮できると思います。日化工場の大きな強みは、一つの生地に対して様々な風合いのものに横展開できるという点です。柔らかさや硬さ、光沢があるものなど同じ生地でも様々なバリエーションの風合いを生み出すことができます。
ポリ乳酸(PLA)でもこれと同じ展開ができるようになれば、もっと世界が広がっていくと考えています。現在は生地に対して、様々な機能性が求められる時代です。その機能が仕上げの整理加工の段階で付加できるというのは我々ソトーの強みです。
(株)ソトー日化工場のシルケット加工用の機械
生地にアルカリを加えることで、滑らかな風合いに仕上げる
藤原 あとはやっぱり、量産化に向けた体制を構築していきたいですね。ポリ乳酸(PLA)は色のコントロールが難しくて、ロット毎に微妙に色が違ってくることが避けられない部分があります。ただ、今後、より多くのお客様に届けられるようにするためには、その誤差がなるべく少なくなるようにしなければいけません。品質の均一化という点にも挑戦していきたいです。
高橋 そうですね。我々としても、ようやくスタートラインにたった段階だと思っています。お客様がポリ乳酸(PLA)であるということを抜きにしても、純粋に生地がよいから選んでいただける、洋服に使いたいと思えるような色や風合いの生地をもっと生み出していきたいです。選んだ生地がたまたまポリ乳酸(PLA)だったら最高だよねという状況をもっともっと、作って行きたいです。