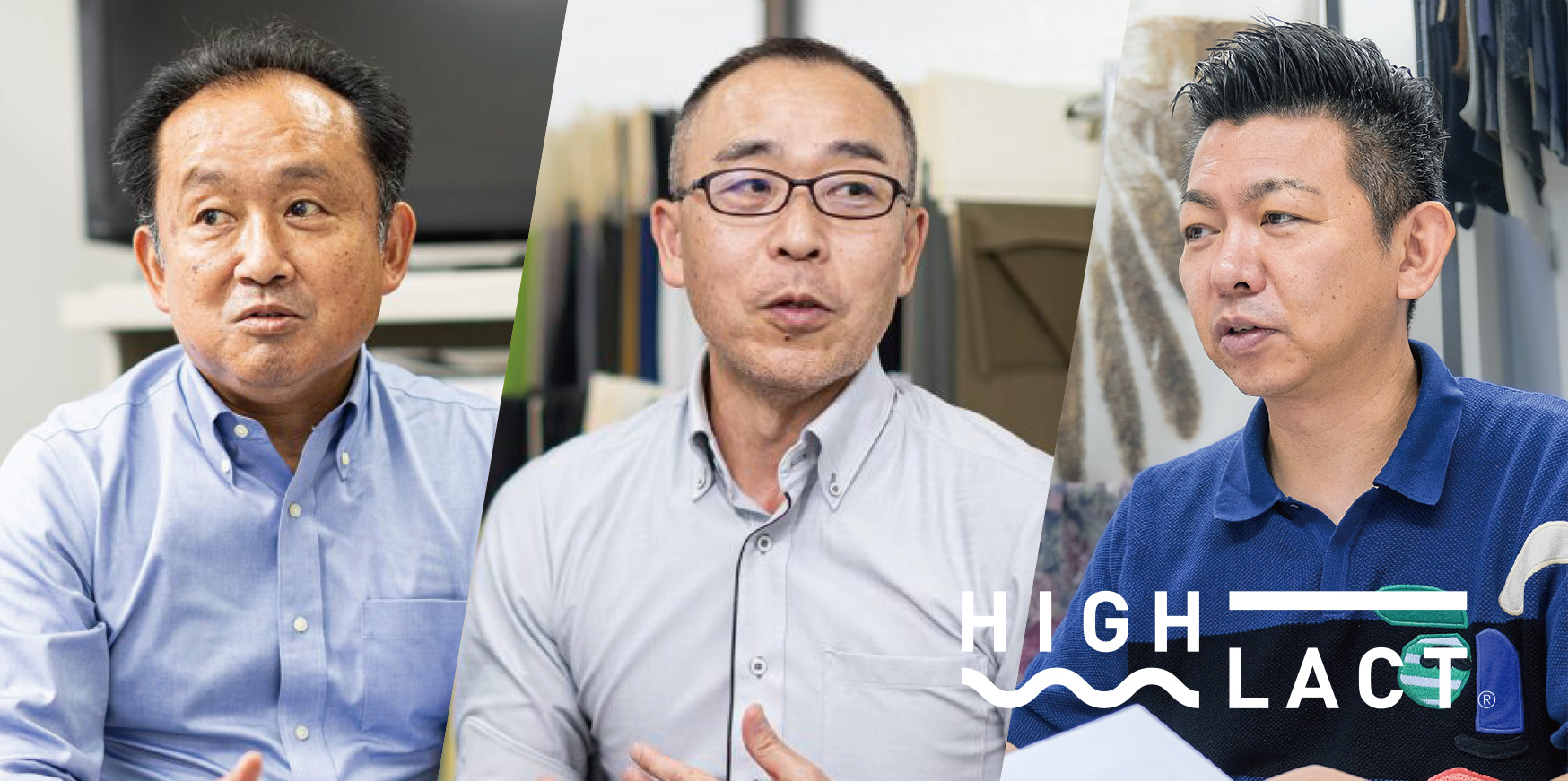
Once deemed impossible, the development of a deep, formal black filament yarn made entirely of PLA100% has been achieved. The key to this successful development lies in the technical prowess of companies that have built a century-long tradition in Japan’s textile industry.
This time, we visited Soto Co., Ltd.'s Nika Factory and interviewed key persons from three companies that played a significant role in the development of HIGHLACT®. We introduce the passion and effort hidden behind the scenes.
Interviewees
Director of the Dyeing and Processing Division, Nika Factory, Naoki Okumura
Company introduction
Founded in 1923. A leading company in the dyeing and finishing industry, deeply rooted in the woolen fabric production area of Owari Ichinomiya for 100 years. At the Nika Factory we visited this time, they carry out dyeing and finishing processing of synthetic fibers such as polyester, wool, and cotton.
Their finishing processing technology, which adds a special texture to the fabric at the same time as dyeing, is highly evaluated both domestically and internationally, and is top-class in the industry.
Managing Director, Yukitaro Takahashi
Company introduction
A venerable textile manufacturer founded in 1924. They constantly produce the highest quality fabric and develop fabric in innovative ways. The ultra-thin cotton fabric “Cosmolama” announced in 2006 was created with a groundbreaking manufacturing method and also obtained a patent. It has been adopted by top maisons around the world.
Product Manager, Fashion & Apparel Division, Sustainability Headquarters, Fujiwara
Company Introduction
A specialized trading company in chemistry that serves as a “bridge between Japan and China”, carrying out import and export sales of chemical products and contract manufacturing business. In addition to developing and marketing new materials, including biodegradable materials, they are also focusing on the development of carbon recycling technology based on C1 chemical technology and licensing business, and the manufacture and sale of catalysts.
——Why did you start working on PLA100% Formal Black with HIGHLACT®?
Fujiwara: To popularize as a fashion fabric, it is essential to be able to express dark colors such as black and navy. More than half of the design of most apparels is composed of black or navy. Therefore, to establish as a fashion fabric, it is not recognized unless black can be expressed.
On the other hand, polylactic acid (PLA) has a characteristic of being weak in high temperatures, and because it is difficult to process at high temperatures, there was the dilemma that the dark colors do not dye well. Therefore, the long-standing fixed concept in the industry was that “black cannot be expressed with polylactic acid (PLA)”. The biggest reason why polylactic acid (PLA) did not spread in fashion was due to dyeing. The desire to somehow break this fixed concept was the trigger for the development of HIGHLACT®’s “PLA100% Formal Black”.
Okumura: In fact, polylactic acid (PLA) fibers have been developed for decades, but at that time there were only white or light colors. Also, there were few samples of 100% PLA filament in the first place, and most of them were mixed with cotton.
——Please tell us about the roles of the three companies in the development of HIGHLACT®’s PLA100% Formal Black.
Fujiwara: HighChem is responsible for procuring raw materials and making yarn. The roles of Ono Baku Industry are fabric design to knitting and making fabric. Then, the fabric manufactured by Ono Baku Industry is dyed and finished at Soto’s Nika Factory, which completes the fabric.
——How did you realize the development of PLA100% Formal Black?
Successful development of a dye exclusive for Polylactic Acid (PLA) realizes a Formal Black recognized by the world!
Okumura: HighChem has added a modifier to polylactic acid (PLA) to improve the heat resistance of the resin, which led us to start working on black dyeing of polylactic acid (PLA). As the temperature increased, the concentration of the dye could be increased, so dyeing was possible to some extent.
Initially, we tried dyeing using a black dye for general polyester. To make the black look deeper, we added a reddish component to the dye and finely mixed in various pigments, which allowed us to take it to the point where it seemed to be the blackest. Even that alone was very surprising that we could dye this much with polylactic acid (PLA).
On the other hand, with polylactic acid (PLA), we could only express a slightly reddish expression compared to the black that polyester and cotton express as formal black. In Europe, if it’s not a black with a strong blue tint, it’s not recognized as formal black.
Fujiwara: Until now, the idea was to use dyes for polyester, etc., for polylactic acid (PLA), but it was not necessarily suitable for polylactic acid (PLA). So, the development of a dye exclusive for polylactic acid (PLA) started.
In developing the dye, we started with the dye manufacturer to develop a dye that suits the modified polylactic acid (PLA), and we proceeded while exchanging opinions in collaboration with Ono Baku Industry and Soto.
The dye manufacturer visited the person in charge of Soto’s Nika Factory many times and conducted repeated experiments in the company’s test room. And finally, after a year of development, we completed this target-close PLA100% Formal Black.
Soto Co., Ltd. Nika Factory’s dyeing machine
Okumura: Yes, at Soto, we have been discussing how to dye and what kind of post-processing is good for the dye exclusive for polylactic acid (PLA).
——Please tell us about the points that Ono Baku Industry and Soto have devised to realize this PLA100% Formal Black.
Takahashi: The point that Ono Baku Industry is particular about when making fabric from yarn is how to bring out the charm of the fabric as a formal black.
Ono Baku Industry is committed to “making good fabric” and strives for first-class manufacturing. Therefore, we add a little extra effort when knitting, such as strengthening the twist of the yarn.
“Ono-style fleece knitting machine”
A knitting machine independently developed by Ono Baku Industry
Takahashi: Especially in 100% synthetic fabrics such as polyester and polylactic acid (PLA), there is a problem that a streak called a horizontal stripe may appear in the horizontal direction. Therefore, by carefully processing in the previous process, we can prevent problems and finish it into a more attractive fabric.
Okumura: When dyeing black fabric, it is necessary to consider color fading that occurs in washing, etc. Polylactic acid (PLA) was not very good at color retention as well as dyeing. We also used Soto’s finishing processing technology for this issue.
To dry the fabric after dyeing, we use a machine called a tenter. Normally, the length of the tenter in a dyeing factory is about 25 meters. However, the normal tenter required high temperature to dry the fabric, which was not suitable for polylactic acid (PLA). In contrast, Soto’s Nika Factory has a tenter that is three times the normal length. This feature is because Owari is a wool-producing area and needs to dry thick wool fabric.
By using this feature, we were able to dry the fabric of polylactic acid (PLA) without using high temperature, which was a great advantage in preventing color fading of PLA100% Formal Black.
“Tenter” used in the process of drying the fabric
Soto Co., Ltd. Nika Factory
——What is the customer’s reaction to PLA100% Formal Black?
Fujiwara: It’s very good. After all, I think that the uniqueness of polylactic acid (PLA), which is different from polyester, comes out in the expression of the fabric by making a filament of PLA100%. It has a bit of drapability and can express a fabric with a silk-like gloss using the filament of polylactic acid (PLA). And I think that the technology that has continued for 100 years by Ono Baku Industry and Soto is the technique that made this possible.
——Please tell us about the future developments.
Okumura: It is to increase the variation of the fabric of polylactic acid (PLA). I think that Soto’s strength can be demonstrated in this regard. A big strength of the Nika Factory is that it can horizontally develop various textures for one fabric. It can produce various variations of texture for the same fabric, such as softness, hardness, and glossy ones.
If the same development can be done with polylactic acid (PLA), I think the world will expand more. Nowadays, various functionalities are required for fabrics. The fact that this function can be added at the stage of finishing processing is our strength at Soto.
“Silk processing machine” at Soto Co., Ltd. Nika Factory
Finish the fabric smoothly by adding alkali
Fujiwara: After all, I want to build a system for mass production. With Polylactic acid (PLA) it is difficult to control the color, and there is an unavoidable part where the color subtly changes for each lot. However, in order to deliver to more customers in the future, we must make sure that the error is as small as possible. I also want to improve the point of quality uniformization.
Takahashi: Yes, we also think that we have just reached the starting line. Even if the customer is polylactic acid (PLA), we want to create more fabrics with colors and textures that make you want to use them for clothes because the fabric is purely good. We want to create more and more situations where the fabric you chose happens to be polylactic acid (PLA).